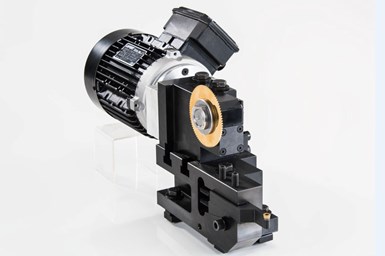
Rotary saw cutting (RSC) using a thin saw blade can save significant material costs compared to traditional single-point cutoff tools. (Photo credits: Watkins Saw Technologies)
If yours is a high-volume machine shop with legacy single- and multi-spindle screw machines, it’s possible you are considering rotary saw cutting (RSC). RSC can be a viable alternative to parting off compared to using a static, single-point cutoff tool. In short, RSC uses a thin, rotating, circular saw blade powered by a motorized attachment to part off turned workpieces while the barstock also rotates.
That said, Dirk Greulich, owner of Watkins Saw Technologies, notes that shops often consider using RSC for parting off only on a job-by-job basis. These are jobs in which parting off is the longest operation, cut flatness is an issue or material costs are very high. However, he suggests that shops can significantly benefit by standardizing on sawing for parting off operations for all work on these machines.
“Standardizing on sawing for parting off can pay dividends for myriad applications,” Greulich maintains. “It breaks down to simple math in terms of potential cost savings.”
He explains that RSC benefits include material savings using a thin saw blade instead of a wider single-point tool, in addition to:
- faster cutting;
- fewer tool changes;
- longer tool life;
- flatter cuts;
- minimal burr and no nib (reducing secondary operations); and
- very small chips.
In fact, given the much smaller kerf produced via sawing, material cost savings can be significant for both inexpensive and expensive barstock materials, he says. (This can range from 5% to 15%.) And while it might seem counterintuitive, higher cost savings come with longer parts because it’s important to consider the number of bars and pounds of material saved, not the percentage.
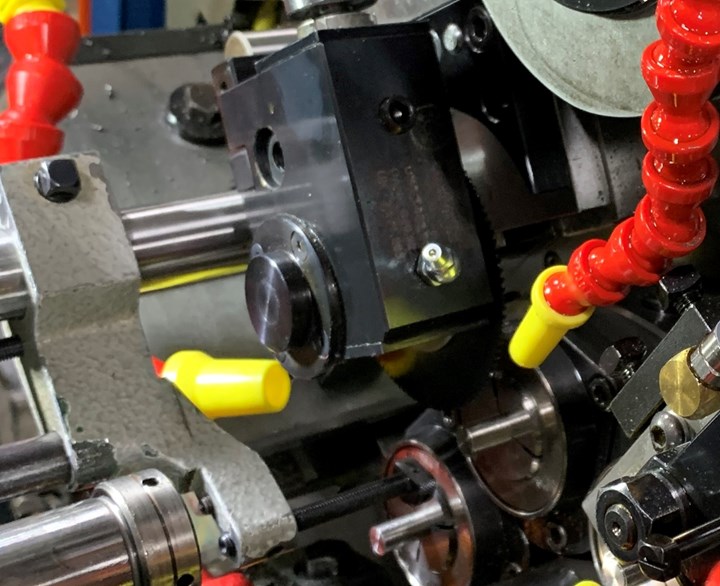
Leasing programs enable shops to realize the benefits of RSC, possibly on multiple machines, at a lower initial cost.
He offers these scenarios to consider for parts with a 12-second cycle produced from 1-inch-diameter 12L14 steel barstock:
- Part length of 0.75-inch: 8.5%/$9,000 material cost savings
- Part length of 1.5-inches: 6%/$12,000 material cost savings
- Part length of 2.5 inches: 3%/$13,000 material cost savings
And, overall, he suggests shops moving to RSC can save an average of $10,000 per machine per shift annually.
Given the much smaller kerf produced via RSC, material cost savings can be significant.
However, Greulich says the upfront cost of the requisite motorized attachment can sometimes be a barrier to entry for RSC. To help mitigate that, Watkins Saw Technologies offers interest-free, monthly financing and leasing programs such as its Kerf Cutter License Program (KCLP). This enables shops to realize the benefits of RSC productivity and performance improvements, possibly on multiple machines, at a lower initial cost (hundreds of dollars monthly compared to a motorized attachment cost that can range from $12,000 to $15,000).
And while these RSC systems are designed for single- and multi-spindle screw machines, the company is looking toward RSC offerings for CNC turning centers with live tooling stations. In this case, a low-cost arbor kit for an interface such as a 5C collet would be used because no motorized attachment would be necessary.
Related Content
4 Strategies for Managing Chip Control
Having strategies in place for managing chips is an important part of protecting the production process, from tool life to product quality.
Read MoreWhat Is Trochoidal Turning? How Might Shops Benefit From It?
While trochoidal milling might be a more well-known toolpath strategy, trochoidal turning can offer similar benefits such as high material removal rates especially for rough-turning operations.
Read MoreData Matrix Codes Offer Cutting Tool Traceability
A company’s quest to discover errors in a manufacturing process has led to printing data matrix codes on its cutting tools that provide a wealth of information for both the user and this cutting tool manufacturer.
Read MoreMicromachining Fundamentals
A number of elements must come together to establish an effective process for machining at a micro level. Here we consider four.
Read MoreRead Next
A Tooling Workshop Worth a Visit
Marubeni Citizen-Cincom’s tooling and accessory workshop offers a chance to learn more about ancillary devices that can boost machining efficiency and capability.
Read More5 Aspects of PMTS I Appreciate
The three-day edition of the 2025 Precision Machining Technology Show kicks off at the start of April. I’ll be there, and here are some reasons why.
Read MoreSeeing Automated Workpiece Measurement in Real Time
User-friendly inspection software for CNC machining centers was shown at IMTS 2024 monitoring measurements between and after machining while performing SPC based on recorded measurement values.
Read More