DyeMansion Powerfuse S PP Smooths 3D Printed Polypropylene
Rapid + TCT 2022: The company specially developed the solvent for polypropylene materials, making the system green as well as biobased to provide economic sustainability.
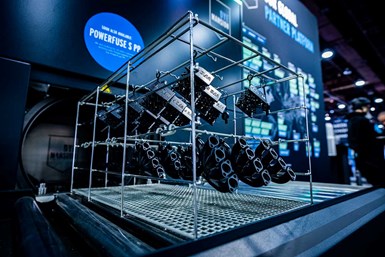
Polypropylene parts finished with DyeMansion’s VaporFuse Surfacing technology in its Power fuse S PP — which the company says is the first industrial solution to smooth 3D printed PP. Photo Credit: DyeMansion
DyeMansion is launching the Powerfuse S PP postprocessing system later this year. It is a special version of its Powerfuse S system which features a VaporFuse Surfacing (VFS) process said to offer a sustainable, industrial vapor polishing system for sealed surfaces. As flexible plastics such as polypropylene (PP) continue to gain relevance, this system is said to enable a variety of new applications and help address the limitation of material availability in additive manufacturing.
It is said the technology behind the Powerfuse S PP is already achieving a PP surface quality standard suitable for today‘s industrial use and is the first system to smooth 3D printed PP. According to the company, vapor polishing improves the mechanical properties of PP parts in which the outcome is sealed, and washable surfaces are visually and functionally on par with injection-molded parts.
The technical specifications of the Powerfuse S PP are nearly identical to the current Powerfuse S version. The company says it specially developed the solvent for PP materials, making the system green as well as biobased to provide economic sustainability. It is also said the solvent has already been successfully tested with all common PP materials on the market so far from HP, BASF, EOS, ALM, Prodways, AM Polymers or Covestro.
With this systems, surfaces are sealed, stable and airtight, the company says. VFS gives additively manufactured plastic parts an injection-molded-like sealed and washable surface. The process is said to reduce surface roughness to a minimum. The entire process chamber is steam flooded under vacuum during each run. This is said to ensure reproducible processing of complex geometries and internal surfaces. It is said VFS is compatible with all common plastics, especially flexible polymers such as TPU, for which mechanical processes are not suitable.