When a Plan Collapses
Not every situation can be anticipated, but if employees are familiar with the best ways to handle issues, even surprises won't be so surprising.
Expect the best, plan for the worst, and prepare to be surprised.
— Denis Waitley
We’ve all experienced that feeling of panic when we have an outline in our heads of how we’re going to approach a situation and suddenly a problem arises that forces us to throw the entire plan out the window. It’s not a pleasant experience, but it happens, and we need to deal with it. Each of us likely faces this issue, at least on some level, every day, perhaps with significant traffic delays on the way to an appointment or the need to make alternate meal plans after burning dinner.
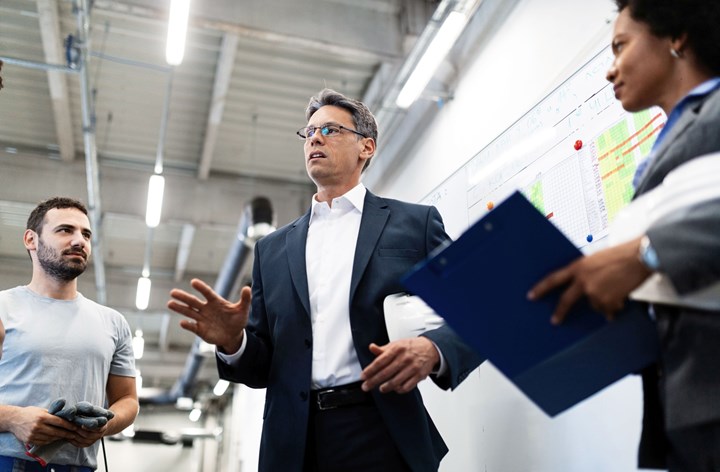
I recently was challenged with a major deadline dilemma when a story lead I was working on fell through at the last minute. I had spent significant time on the story, including researching the technology, lining up the appropriate people with whom to speak, traveling to the shop to see first-hand the cool advances they have made in their production processes, and writing the manuscript. Everything seemed to be going as planned—until it wasn’t.
When I sent the article draft out for the shop to review, management had a change of heart regarding what information they were willing to divulge. In short, they decided they didn’t want to divulge anything.
In theory, having already attained the information, I suppose I could have run the story anyway. But as a trade journalist, that’s not our style. When we develop content for the magazine, we have everyone’s best interest in mind. Most important, we want to provide useful information to our readers, but we also want the shops that we write about, as well as their suppliers, to find some benefit from getting their names out there through this information exchange. It certainly does us no good to burn bridges, and the problems that doing so may create could also indirectly and negatively affect our readers.
Rather than dwelling on the concerns of the shop, because my deadline was now quickly approaching I instead needed to switch direction and hammer out Plan B for the article. This situation was not unprecedented, so we knew the advantages of being prepared. Fortunately, we had another article partially developed that we could quickly complete and plug into the recently vacated spot. The contingency plan served its purpose—the new article was placed, and the magazine was delivered on time.
Do you have contingency plans in place and have you reviewed them lately? Some situations are so common that the backup plans seem obvious. Perhaps personnel are cross-trained to be able to fill in when someone is sick or on vacation. Sufficient tooling inventory and certain machine parts are kept on-hand for quick replacement in case equipment failure occurs. But what about less common but more significant crises?
What if a machine suddenly is out of commission long-term? What if that customer who represents 50 percent of your business decides to go a different route? What if your facility is damaged by fire or natural disaster? Companies need to be prepared for situations of varying degrees because they never know what problems they may end up facing.
By considering the scenarios that could jeopardize your company’s day-to-day operations and developing sufficient responses to those scenarios, you’ll better position your organization to overcome inevitable adversity. Having a knowledgeable team in place that understands the potential risks and can assemble reasonable plans of action for various situations creates a basis for problem resolution. And just like an athlete or musician or anyone else who needs to be able to perform under pressure, occasionally practicing crisis control plan procedures sets the company up for fast and effective response. Not every situation can be anticipated, but if employees are familiar with the best ways to handle issues, even surprises won’t be so surprising.
Next time a customer’s unreasonable demands throw a wrench into your schedule, or one of your vendors fails to supply the service you desperately need, or you find your current shopfloor employees are lacking sufficient knowledge to get the next family of parts out the door, perhaps you’ll be prepared with a Plan B that easily relieves the situation and allows you to quickly return to business
as usual.
Read Next
A Tooling Workshop Worth a Visit
Marubeni Citizen-Cincom’s tooling and accessory workshop offers a chance to learn more about ancillary devices that can boost machining efficiency and capability.
Read MoreSeeing Automated Workpiece Measurement in Real Time
User-friendly inspection software for CNC machining centers was shown at IMTS 2024 monitoring measurements between and after machining while performing SPC based on recorded measurement values.
Read More5 Aspects of PMTS I Appreciate
The three-day edition of the 2025 Precision Machining Technology Show kicks off at the start of April. I’ll be there, and here are some reasons why.
Read More