Vision’s LVC200 Measures Large Pieces, Multiple Small Components
Automated video measurement system’s features include advanced video edge detection, easy reporting and data export, DXF overlays and profile fitting, with a thread measurement option.
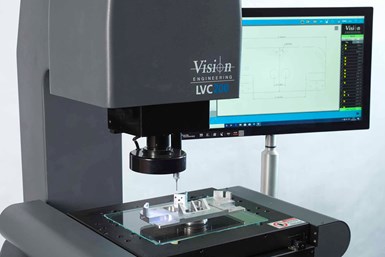
LVC200 measuring a metal part.
Vision Engineering is broadening its range of LVC automated video measurement systems with the addition of the LVC200 and higher specification variants. The LVC200 is well suited for measuring large components or multiple small components, quickly, easily and accurately.
According to the company, the LVC range is easy to use and offers a choice of measuring capacities and fully automated movement in all three axes, making component measurement faster. Nonstop measurement routines are possible through programs which can have magnification changes built in. Also, multiple components can be loaded onto the stage and measured easily and automatically in a single program. The system is pre-programmable or can be joystick driven for quick, one-off measurements.
The LVC series offers accurate measurements via its 5 or 6.4 MP cameras, granite and aluminum bases for extra stability, and precision-stage 6.5:1 or 12:1 motorized zoom. LVC supports the use of a touch probe in all three axes, for a wide range of industrial measurement applications, including precision machining, casting, plastic molding, electronics and medical devices.
The company says the LVC is supplied with easy-to-use, highly intuitive M3 software, offering an extensive suite of measurement functions. M3’s key features include advanced video edge detection, easy reporting and data export, DXF overlays and profile fitting, with a thread measurement option.
Plus models include 6.4 MP cameras, 12:1 motorized zoom objective for a broader magnification range and up to 700X magnification range.
Related Content
-
The Advantages of Automated Shopfloor Gaging
This “parallel kinematic” gage offers the opportunity to automate and improve machining process control for shops endeavoring to move from sample inspection to 100% inspection.
-
The Value of CMM Controller Retrofits
In this case, new controllers for two coordinate measuring machines — one 26 years old — with new programming software offers the possibility to enable multisensor inspection of critical, turned aerospace components.
-
Replace Repetitive Measurement With DIY Robotic Automation
After minimal training, a shop can learn how to use this robotic inspection system configured for a shopfloor application to supersede repetitive, time-consuming, high-mix gaging processes. It can then be redeployed for another application somewhere else in the facility.