Video: Avoiding Separation Anxiety
It’s good to know how far a lubricants developer for machine tools goes to make sure oil will not separate from grease. Here is how one such company ensures the quality of its product.
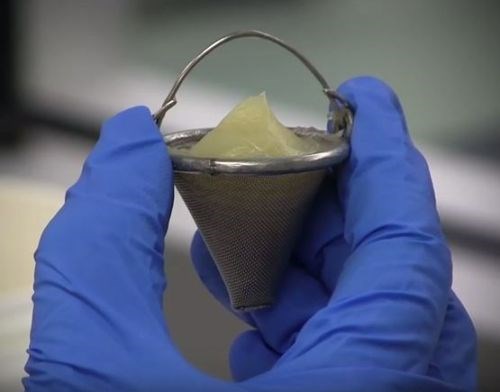
Oil separating from the grease in machine tool lubricants can be a problem in high heat situations, especially during storage. That’s why it’s reassuring to know that companies such as Nye Lubricants perform oil separation tests on its products prior to shipping.
This video features the test, also known as ASTM method D-6184. This test is one of the four required tests performed on all greases at Nye by the Quality Release Team prior to shipping the product to customers.
An oil separation test monitors the separation of oil from grease at elevated temperatures for a defined period of time. The tendency of oil to separate during storage can be an important characteristic. When the base oil begins to separate from other raw materials in grease, the remaining material may change in consistency and potentially affect the ability of the grease to function as designed.
The test begins with a technician weighing the empty oil separation apparatus on a scale that follows ASTM method specifications and recording the value. Next, the technician weighs and records the empty beaker of the oil separation apparatus. The cone screen is then filled with 10 grams of grease, ± 0.01 gram. Both the filled cone and the empty oil separation apparatus are weighed to ensure the proper amount of grease was put in the cone. The cone is placed on the lid of the oil separation apparatus and then re-weighed.
When ready, the entire apparatus is heated in an oven at a specified temperature ranging from 100°C to 204°C, ± 1°C, for 24 hours, ± 5 minutes. Both the time and temperature conditions can be adjusted according to the product application.
At the end of this heating period, the technician will remove the apparatus and weigh the beaker containing any separated oil. The previously determined empty beaker weight is then subtracted from the weight of the beaker containing oil, divided by the original grease weight, and multiplied by 100 for a percentage result.
The oil is the primary lubricating component of the grease. Depending on the application, some oil separation is desirable and necessary. In these specific applications, the deliberate design of oil separation will make the oil available to critical component surfaces.
Test results can distinguish between greases that will either promote or resist oil separation. However, results obtained with this procedure are not intended to predict oil separation tendencies of grease under dynamic service conditions.