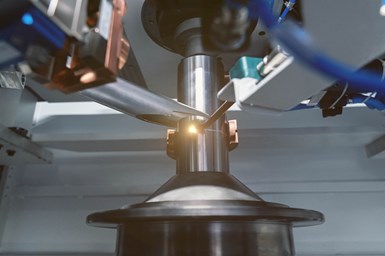
During the welding process on the ELC 6, the vertically arranged workpiece rotates. The precisely meterable energy of the laser beam allows a high welding speed. (Photo credits: Emag LLC)
Rotor shafts are key components for electric vehicle (EV) motors. Automotive production planners continuously focus their efforts on establishing effective design and manufacturing processes to produce them.
Hollow components provide design freedom, less weight and lower material costs for assembled rotor shafts. Still, this “heart” of an electric motor must withstand particularly high loads as motor speeds as high as 20,000 rpm are now possible. Compared to a camshaft in an internal combustion engine, for example, this value is many times higher. Thus, the production of assembled rotor shafts is always about manufacturing tolerance because even minimal imbalances must be avoided at all costs because they could reduce motor life.
Emag LaserTec offers an automated solution to “build” two-piece rotor shafts to support the growing EV market based on its Emag Laser Cell (ELC 6) laser welding machine. In addition to the machine, the process includes part handling, preheating and joining as well as a rotary table to enable timed welding operations to take place in fast succession.
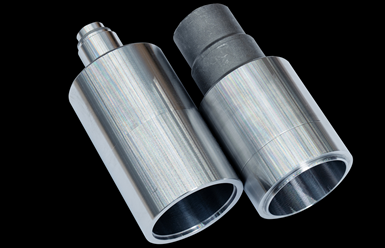
For rotor shafts, hollow components provide less weight and lower material costs.
The precisely metered, concentrated energy of the laser beam permits high welding speeds with minimal distortion on the welded component, the company says. A look at the details reveals the performance of the machine, which was specially developed for powertrain components with circumferential welds:
- Before the individual parts are loaded into the ELC 6, the workpieces are cleaned using a laser. For this purpose, Emag LaserTec offers the LC 4 laser cleaning machine, which can be optimally link with the ELC 6 to offer seamless line integration.
- Preheating and joining occur in the next step in the ELC 6. The induction technology first ensures an optimal processing temperature on the component before the two components are joined.
- Before welding, the weld seam position is verified and the component position is readjusted as necessary. The contour is scanned and the data is communicated to the welding optics and the NC axes.
- During the subsequent welding process, the vertically arranged workpiece rotates, while the laser optics move only radially towards the workpiece. The welding process with its focused energy thus takes place virtually from the side at the circumferential weld. A pyrometer controls the process temperature.
- After welding, the component is transported out of the machine by a swiveling motion of the rotary table and unloaded by a robot.
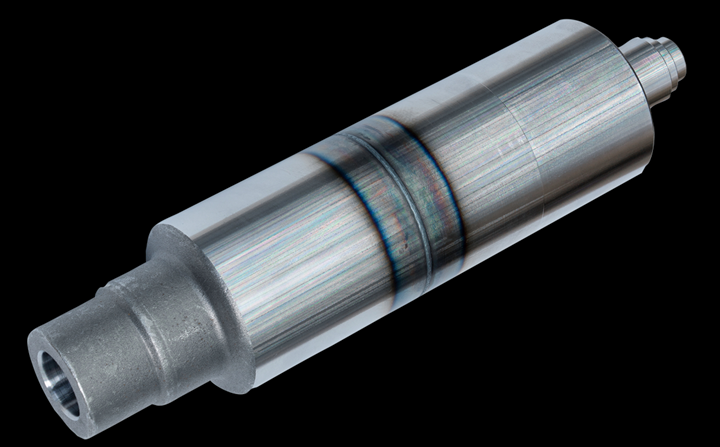
This rotor shaft design provides developers a great deal of design freedom.
Overall, this solution provides high production speed in part because the machine with its rotary table is loaded and unloaded during welding (and is thus cycle time-concurrent). In addition, the individual subprocesses are synchronized. The “fixed optics/moving workpiece” principle was created to help ensure a high level of operational reliability. In addition, Emag LaserTec designs this solution very flexibly for customers in terms of technology, output and automation, whereby workpieces with a maximum height and external of 300 millimeters can be welded in the ELC 6.
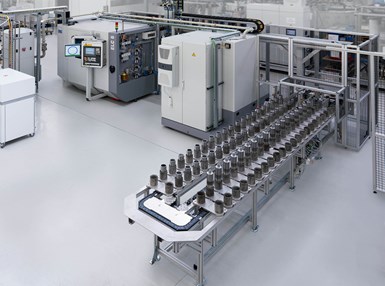
The ELC 6 was specially developed for automated, high-volume production of rotor shafts for EV motors.
Emag has also developed related solutions such as the subsequent joining of the rotor shaft and rotor-sheet package as well as precision overturning of this package. The same applies to the turning, gear cutting and grinding of the two individual rotor shaft parts before welding.
When it comes to the automation technology for effective transport between the machines, the company says it adapts to its customers’ ideas. For example, line gantries, stacking cells, accumulating conveyors or its own TrackMotion system can be used. These systems benefit from the uniformity of the machines used with their optimized interfaces. And, as a result, Emag says it is the only contact required during planning, implementation and servicing.
Related Content
Simulated Complete Machining of EV Aluminum Inverter Cases
At EMO 2023 in Hannover, Germany, FANUC presented an automated manufacturing cell simulating the complete production and measurement of aluminum electric vehicle (EV) inverter cases.
Read MoreThyssenkrupp Materials Services Opens New Facility in Texas
The new service center in Sinton, Texas supports the materials and supply chain management needs of manufacturing companies across multiple markets in the region.
Read MoreHow Small Machine Shops Can Fight Supply Chain Problems
Supply chain disruptions are still presenting challenges in manufacturing. This article examines the effects on aerospace, automotive and medical industries. It also covers ways that machine shops can be successful securing work despite the challenges created by the supply chain.
Read MoreT&H Lemont Reaches Quality Assurance Milestone
The company’s quality management system has provided a solid year with no defects, rejects or recalls.
Read MoreRead Next
Do You Have Single Points of Failure?
Plans need to be in place before a catastrophic event occurs.
Read MoreA Tooling Workshop Worth a Visit
Marubeni Citizen-Cincom’s tooling and accessory workshop offers a chance to learn more about ancillary devices that can boost machining efficiency and capability.
Read MoreEmerging Leaders Nominations Now Open
Here’s your chance to highlight a young person in your manufacturing business who is on the path to be a future leader moving your company forward.
Read More