Improve Energy Savings and Efficiency with Vector Kinematics
The rocking, rotational nozzle movement performed by vector kinematics spray cleaning technology combined with temperature and cleaning additives provides an effective, fast and economical parts cleaning process.
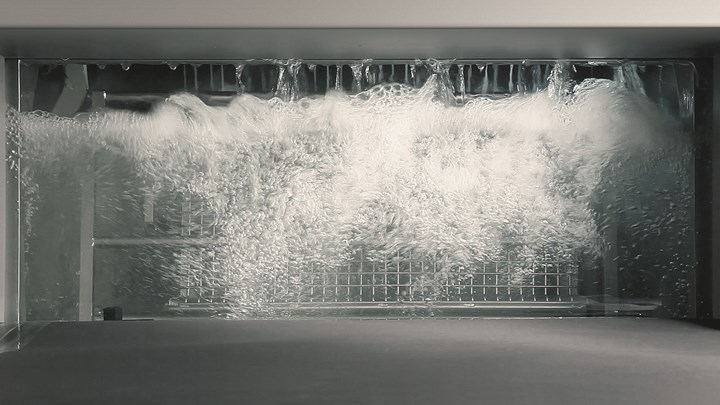
Mafac’s vector kinematics cleaning system is designed with the notion that the more motion taking place while cleaning, the better the cleaning process. (All photos courtesy of Mafac.)
“There’s always room for improvement” is a mantra that Mafac, a German manufacturer of aqueous parts cleaning equipment, has taken to heart. The company recently upgraded its kinematic cleaning technology to a vector kinematics process, which it says creates an even more effective way to spray clean machined metal parts, especially those with blind holes and recesses that are often difficult to clean with other techniques. Because its vector kinematic process results in faster cleaning and drying times, the company, whose cleaning machines are distributed in the U.S. by Jayco Cleaning Technologies, says these cleaning systems can enhance cleaning effectiveness and save users up to 20% in energy usage.
Cleaning on the Move
Mafac believes that the more motion taking place within the cleaning process, the better. Therefore, its latest vector kinematics process includes even more movement for cleaning and drying components. In contrast to the process using a conventional nozzle system, the workpieces being cleaned with the vector kinematics method are not hit at a specific angle. Instead, the nozzle tube performs a rocking, rotational movement 35 degrees to either side, while the basket receptacle system rotates synchronously at an adapted speed.
“The best way to explain vector kinematics is to liken the principle of this motion to what one would see when trying to clean complex objects,” says Jay Nawani, CEO, Jayco Cleaning Technologies. “When brushing one’s teeth, it is always helpful to swivel your wrist instead of doing just one straight line motion. Also, when hand washing anything critical or complex with a brush, you would naturally get better cleaning results if you were to swivel or gently rock the cleaning brush when moving it across the area being cleaned.”
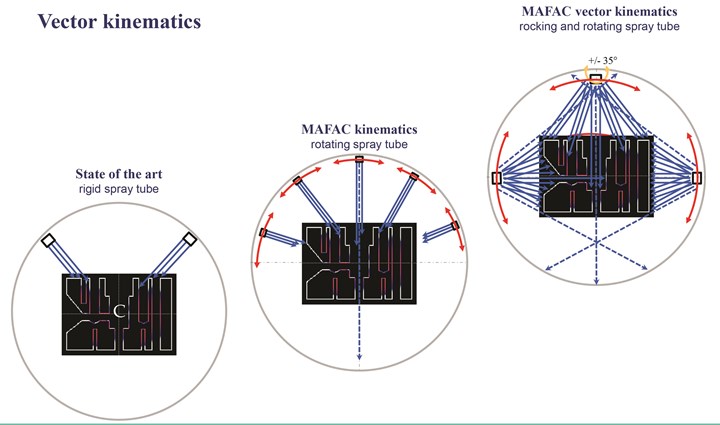
In contrast to the process using a conventional nozzle system, the workpieces being cleaned with the vector kinematics method are not hit at a specific angle. Instead, the nozzle tube performs a rocking, rotational movement 35 degrees to either side, while the basket receptacle system rotates synchronously at an adapted speed.
Similarly, Mafac’s technology is within a rotary basket machine where vector kinematics allows the cleaning spray nozzles to additionally swivel, providing its signature rocking motion.
Proper basket rotation is also a key part of the system. According to Nawani, there are several factors that must be taken into consideration when selecting the right basket and spray manifold rotation for a critical cleaning process. These include:
- Whether a part has blind holes or other deep machined features on multiple faces;
- Importance of machined surface finish;
- Machined parts that are bulk loaded in the basket;
- Number of parts in the basket;
- Size and weight of parts; and
- Importance of cleaning and drying processes.
Workpieces with complex geometries such as cross-drilled holes and undercuts, in particular, are said to benefit from the targeted turbulence of Mafac vector kinematics. The diagram below compares the areas of a part that are cleaned when using a conventional nozzle system as well as the vector kinematics process. The vector kinematics system process clearly reaches more regions than its conventional counterpart.
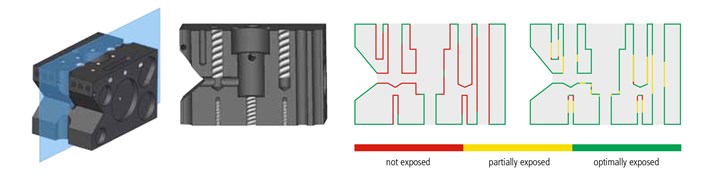
This diagram shows the areas of the part that are not exposed, partially exposed and fully exposed to the vector kinematics cleaning process. Optimally (green) and partially (yellow) exposed regions clearly outweigh unreached locations (red).
Although considered aqueous, the vector kinematics process sometimes uses small amounts of chemical cleaning agents, about 1% to 5%. But there are also applications where no chemicals are needed and only water is used. The type of chemistry used depends on the base metal of the part being cleaned, type of contamination and level of cleanliness required.
Programming Process
The machine’s Maviatic visual display software controller, developed by Mafac, calculates the movement of the basket rotation beforehand, making possible corotation and counterrotation with respect to the nozzle tube. This coordinated movement of the nozzle tube and basket can result, depending on the part geometry, in up to 60% more contact on the component surfaces, thus providing a significantly cleaner part that is more likely to satisfy stringent cleanliness specifications.
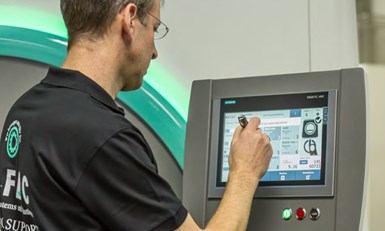
Prior to programming, the machine operator must create a cleaning process “recipe” that is needed to clean and dry the parts. The recipe includes process temperatures, wash process, wash time and basket motion, rinse time, drying process, drying time and basket motion.
Prior to programming, the machine operator must create a cleaning process “recipe” that is needed to clean and dry the parts, according to Nawani. The recipe is put into the touchscreen controller using guided prompts. Typically, this involves selecting:
- Process temperatures. These temperatures range from about 120°F to 170°F. The average temperature is about 150°F.
- Wash process, including spray, turbulation and ultrasonics.
- The wash time and basket motion (basket rotation, swiveling motion) and spray header rotation.
- Rinse process, including spray, turbulation and ultrasonics.
- The rinse time and basket motion (basket rotation, swiveling motion) and spray header rotation.
- The drying process (compressed air blow-off, hot air dry or vacuum dry).
- The drying time and basket motion (basket rotation, swiveling motion) and spray header rotation.
Depending on the equipment configuration and options selected, the nozzle pressure can be fixed or variable, ranging from about 15 to 250 psi. In the case of variable pressure, even the operating pressure can be set as part of the cleaning process recipe, where the pressure is lower for more delicate parts and higher for tough-to-clean parts that have complex machined features.
Time Savings
Vector kinematics technology offers the combination of mechanical components, temperature, cleaning additives and time savings which, in turn, can provide an effective and economical parts cleaning process.
Because of the simultaneous nozzle tube rocking movement and the basket receptacle rotation, vector kinematics is said to deliver cleaner parts in a shorter amount of time or cleaner parts within the same specified time compared with processes that only use spray tubes or rotational spray tubes. In fact, the drying process also uses the vector kinematic system with the moving nozzles achieving a higher heat and material exchange.
The entire cleaning, rinsing and drying cycles are complete on an average of 10 minutes per batch, but this process time can land anywhere between seven and 20 minutes.
Jayco Cleaning Technologies | (513) 737-9600 | jaycoclean.com
Related Content
Kyzen Solvents Provide Ease of Cleaning for Medical Parts
The Metalnox line of solvent products are designed to improve reliability and increase the ease of cleaning in vacuum and vapor degreasing processes.
Read MoreA ‘Clean’ Agenda Offers Unique Presentations in Chicago
The 2024 Parts Cleaning Conference, co-located with the International Manufacturing Technology Show, includes presentations by several speakers who are new to the conference and topics that have not been covered in past editions of this event.
Read MoreMeeting Stringent Cleaning Goals With Modular Ultrasonic System
A knee implant manufacturer implements an advanced cleaning system that meets its tight cleaning requirements, including documenting, validating and tracing the entire cleaning process.
Read MoreVersatile Sandblasting for Deburring Intricate Geometries
PMTS 2023: Comco’s MicroBlasting sandblasting systems can deburr, texture and clean small, intricate parts.
Read MoreRead Next
Aqueous Cleaning Optimization
David Gotoff, product manager at Chemetall, explains how each area of an aqueous process must be optimized, including system design and mechanical action, chemistry selection, key performance indicators, soil management, maintenance, rust protection, rust preventive selection, water chemistry, and drying.
Read More5 Aspects of PMTS I Appreciate
The three-day edition of the 2025 Precision Machining Technology Show kicks off at the start of April. I’ll be there, and here are some reasons why.
Read MoreDo You Have Single Points of Failure?
Plans need to be in place before a catastrophic event occurs.
Read More