Record Number of Certifications Pursued for Metalworking Jobs
NIMS announced that it awarded a record number of credentials last year to individuals seeking to enter into or advance in jobs in the metalworking industry.
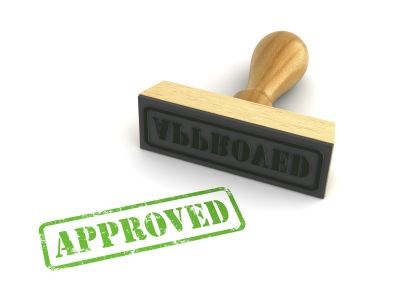
The National Institute for Metalworking Skills (NIMS), a standards and skill certification body for metalworking, announced that it awarded a record number of credentials last year to individuals seeking to enter into or advance in jobs in the industry. In 2014, NIMS issued 18,947 industry-recognized credentials, representing a 36-percent increase from 2013.
“It is clear that the precision manufacturing sector is strong and growing, and more students and workers are preparing for success in the wide variety of jobs our industry offers,” says Jim Wall, executive director of NIMS. “NIMS would like to congratulate more than 8,000 individuals who earned at least one industry-recognized credential last year and have the ‘mark of excellence’ that will make them highly sought-after talent.”
More than 6,000 metalworking companies and major industry trade associations have invested more than $7.5 million in private funds to develop NIMS standards and credentials that prepare and advance the industry’s workforce and continue to upgrade and maintain the standards as the industry changes.
“The precision manufacturing industry is constantly evolving, becoming more complex, technology-driven and innovative,” says Greg Chambers, director of compliance, Oberg Industries, Inc., and chairman of the board at NIMS. “NIMS ensures that companies, workers, and students keep up with changing industry standards and job requirements and that training programs equip individuals with the knowledge, skills and abilities they need to succeed in in-demand jobs.”
NIMS has developed skills standards ranging from entry-level to master-level that cover the breadth of metalworking operations, including metalforming and machining. NIMS certifies individuals’ skills against these national standards via credentials that companies can use to recruit, hire, place, and promote individual workers. Training programs, both at the secondary and post-secondary level, incorporate the credentials as performance or completion measures of academic coursework in metalforming or machining programs.
Related Content
-
Recognizing Signs of a Degrading Workplace Culture
Is your machine shop missing key “culture elements?” Here are ways to identify if your organization is heading in the right or wrong direction in terms of establishing a healthy company culture.
-
2023 Emerging Leaders Strengthen Their Staffs, Solve Problems
Superb critical thinking, top-notch leadership skills and a passion for building a strong team are a few of the common traits held by this year’s five Production Machining Emerging Leader award winners.
-
Manufacturing Skills Training: Virginia Martinez and Laiken Carrillo
Roles of Women in Manufacturing Series: A precision machining career starts with skills. Virginia and Laiken share their journey and how they help prepare the next generation.