Customizable, Flexible Tool Setting for Improved In-Machine Inspections
Hexagon’s m&h R-400 multi-sensor radio probe system is designed to improve ease of in-machine measurement configuration and handling in a range of manufacturing environments.
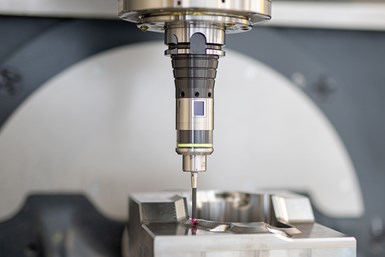
Hexagon’s m&h R-400 multisensor radio probe system
Hexagon’s m&h R-400 multisensor radio probe system offers a variety of probing and tool setting options for manufacturers looking for efficiency gains in a variety of production environments. Its multisensor in-machine tool measurement capabilities include compact tactile radio probes and a flexible tool setter that can be used interchangeably to identify and correct production problems early in the production process.
The system can be used to fulfill both in-machine workpiece measurement and tool setting requirements. The system can be used for a variety of purposes, including machining setups with any machine tool, highly accurate measurement of complex free-form geometries with tight tolerances and the checking of machine kinematics, the company says
The tactile probe system includes a built-in display, providing status data at a glance which enables users to save or load settings, and makes it easy to switch between tactile-sensor and tool setting functions. Designed for flexible in-machine measurement, the system can be used as a radio probe by equipping it with a probe shank or as a radio tool setter by mounting it on a tool setter base.
The system features an illuminated ring that completely surrounds the probe body and lights up to indicate current performance conditions and activities, so operators can easily see the system status. The indicator ring notifications include “system ready,” “battery low” and “probing” to increase shop-floor efficiency by providing immediate access to information that benefits workflow.
The probe is designed to perform with precision in tight spaces and is available with three different measuring units. Additionally, an extension of up to 200 mm in length can be used to bring the measuring unit closer to the measurement area. The probe is said to be compact with a diameter of only 40 mm, enabling it to fit into almost any tool magazine and making it well suited for use on small machines or applications with limited space, the company says.
Related Content
-
How Well do You Know Granite Surface Plates?
Here are some tips for choosing, maintaining and customizing a granite solution that will best meet your shop’s particular inspection needs.
-
Addressing Machining’s Necessary Evil
Many view quality control as such, but integrating new measurement technologies and approaches can ultimately minimize QC’s impact on throughput and a company’s bottom line.
-
Automated Inspection Transforms Medical Manufacturer’s Quality Control
Manual steps for part inspection have been eliminated with a new CMM process using more advanced software and strategies such as using a combined scanning/touch-trigger probe.